The health and safety of your employees is not something to be taken lightly. Workplace accidents can happen in the blink of an eye and when you least expect it. Some can be easily identified and avoided, while others can potentially create dangerous situations for everyone. Because the risk of injury is always present, employers have to take a proactive approach when it comes to protecting their staff from any and all hazards. When you have worker's lives in your hands, you can never take too many precautions. It's important to not only provide the proper safety equipment for your staff, but to also educate and inform everyone on up to date safety standards and procedures. Here at Texas America Safety Company (T.A.S.C.O.), we specialize in numerous safety supplies and have been experts in the field of safety for more than twenty years. Our goal is to keep you and your staff safe on the job with the most up to date, state of the art safety supplies.
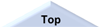
Safety Postings When working in a potentially hazardous zone, being aware of the potential hazards around you could save your life. Being aware of things such as safety postings or signage may seem like a waste of time, but they can actually provide you with very helpful information. Safety postings aren't just posted because they're required. They're there for your safety. These signs are there to identify hazards and visually communicate important safety information. You've probably seen a safety posting or two in your time and never really given much thought to it, but OSHA (Occupational Safety and Health Administration) has three different classifications of signs: danger signs, caution signs, and safety instruction signs.
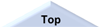
Danger Signs OSHA defines danger signs as a sign that indicates immediate danger and special precautions are necessary. These signs must also be red, white, and black. A danger site might look like this...
Caution Signs
OSHA defines caution signs as a warning to people against potential hazards or caution against unsafe practices. These signs will typically have a yellow background, black panel and yellow letters. If there is a yellow background, the letter must be black. A caution sign might look like this...
Safety Instruction Signs Safety instruction signs are defined by OSHA as signs that are used when there is a need for general instructions and suggestions related to safety measures. The colors used for these signs are a white background with black lettering, and green panels and white lettering. Here is an example of a safety instruction sign:
|
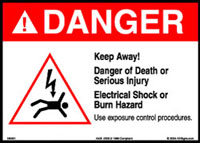
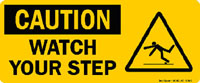
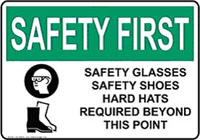
|
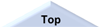
Certifications Along with safety postings, it's extremely important to have all of your certifications done before attempting any hazardous job. According to the Board of Certified Safety Professionals (BCSP), there are about three hundred health, environment, and ergonomics certification programs available in the United States today, all of which vary depending on the industry you're in. The most common safety certification is the CSP (certified safety professional). In order to gain this certification, you must have or do the following:
- Associate's degree in safety and health or an accredited Bachelor's degree in any field
- Four or more years of professional safety experience
- Pass the Safety Fundamentals and/or Comprehensive Practice exams.
Before attempting to gain certifications though, it's critical to ensure that the certifications are being issued by organizations that are reputable in the field of safety. A few questions you should ask are:
- Has the organization existed for at least 5 years?
- Is it accredited by nationally recognized accredited bodies such as the National Commission for Certifying Agencies (NCCA)?
- Is their information up to date?
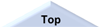
Health Hazards Aside from any immediate physical danger, employers should also keep in mind that the environment their workers are working in may pose a threat to them down the road. Regardless of the type of work or industry you're in, you have to make sure that the work environment is clean and free from any potentially life threatening things, such as asbestos, undetected gas or even chemical spills. To start, regularly clean the floor, dust where you can, remove trash and make sure the air is clean. Keeping an eye out for something more serious like asbestos can be a bit more involved, but it should not be taken lightly. Exposure to asbestos has lead many people to develop mesothelioma and it is reported that there was an average of 12.8 deaths per million people annually between 1999 and 2010. If you think you are in danger of being exposed to asbestos, you need to inform your employer immediately.
Asbestos isn't the only health hazard to keep an eye out for though. Something as simple as bacteria on surfaces has been resulting in many hospital visits for many people. Keeping your workplace clean and safe has never been more important. If you work in a job that requires you to come into contact with chemicals such as gasoline, paint, bleach, kerosene, or pesticides, it can be a major risk to your health. Daily exposure to such chemicals has been linked to an increase risk of cancer, especially if the chemicals are inhaled or ingested. It is because of this that providing proper safety equipment, such as eye goggles, hazmat suits, masks and gloves to your workers is of the utmost importance. Safety is and should always be your number one priority.
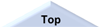
General Safety Standards Safety standards are designed to ensure the safety of products, activities or processes. They may be advisory or compulsory and are normally laid down by an advisory or regulatory body that may be either voluntary or statutory. There are many different types of safety standards for every industry, from food service all the way to the road safety commission. Many industries have different groups that oversee their safety standards to ensure the safety of every person involved. Groups such as OSHA oversee the safety of employees in their work environment. That can mean making sure they are wearing the proper safety equipment to making sure they are working in a safe environment. Everyone has the right to work in a safe workplace and have access to proper safety equipment. Companies need to be aware of the standards for their industry; not knowing about a certain standard is not an excuse that will be tolerated. If they do not abide by any of the standards they run the risk of getting fined or shut down. Employers need to be diligent about keeping up with the ever changing standards and make an effort to make sure they are running a safe business. Safety equipment also needs to be properly maintained and updated, to abide by the standards.
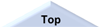
Medical Surveillance Medical surveillance is the systematic assessment of employees exposed or potentially exposed to occupational hazards. This assessment monitors individuals for adverse health effects and determines the effectiveness of exposure prevention strategies. This involves collecting and interpreting data to detect changes in the health status of employees that have been potentially exposed to hazardous substances. It is important to monitor potential occupational hazards in the work environment to ensure the safety of all of the employees.
It is very important to be proactive in this area. Checking for possible risk is crucial in identifying any problems early on. The things that need to be checked are: the type of work performed, the duration of the task, the materials being sued, and the potential for harmful exposure. Many times the surveillance will take place by performing medical exams on employees. The actual results are kept confidential between the employee and doctor but the doctor will report recommendations based on the findings of the medical testing.
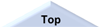
Lead Controls Lead is a heavy metal that has been poisoning workers for many years. Lead poisoning is very dangerous and can lead to the damage of the central nervous system, reproductive system, cardiovascular system, hematological system and the kidneys. Short-term exposure can cause damage for a few days or weeks, but can also lead to serious issues in the future. Lead exposure becomes a much more serious problem when the exposure becomes long-term. The most common way lead gets into the body is through inhalation from dust, fumes or mist. After the lead gets into the lungs it can travel through the bloodstream and become stored in various organs and body tissues. If the lead does get into the body's tissue, it may then start to cause irreversible damage to the body. Due to the severity of working with lead it is important that employers take all the right steps in protecting their employees. You can do things such as:
- Provide protective clothing and equipment
- Conduct medical surveillance
- Provide hygiene facilities
- Display proper signage
- Provide employee training
- Keep proper records
Make sure, as an employer that all the correct steps are taken to ensure the protection of each employee. If any incidents do arise, make sure that proper records are kept and the incident is investigated to determine the cause of the exposure, especially if all safety measures were in place.
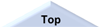
Communication It is extremely important to have open lines of communication about the health hazards and safety standards in each work environment. The best way to keep everyone safe is to inform every employee of the possible dangers. With proper two-way communication all employees will feel comfortable coming to management with problems they see arising. This can help stop a health hazard from becoming dangerous. If employees don't feel they can effectively communicate with management they may overlook safety measures and not report when there is a problem with one of the safety protocols. Without that line of communication management might not be aware of the dangers that are happening on the front lines of the work place. Communication doesn't always need to be verbal. Having proper signage is also vital to ensuring the safety of all staff. Posting directions on how to use heavy equipment, or having a list of the proper safety gear to be worn are very important signs to have. Sometimes it may seem redundant to have such signs, but they serve as a great reminder to employees. Besides having signage around the workplace, having safety manuals readily available is also very important. These manuals can explain how to use a certain tool or material and it can also explain what to do in case of an emergency with said tool or material. Manuals are a great educational tool that should be available to anyone working in an environment with potential hazards. Keeping everyone informed and aware is the best safety prevention.
Safety Standards for Preparation It is important to be prepared and up to date on all of the safety standards for your industry. Once you have made yourself aware of the proper standards, it is crucial that you implement those standards. Here are three key safety standards as examples:
- Placing appropriate safety signage
- Properly training staff
- Providing proper safety equipment
Proper Safety Supplies When working in a hazardous environment, it is very important to wear the proper safety supplies and to have them readily available for everyone who will need them. It is also crucial that everyone is trained on how to wear and use safety supplies. Some of the most popular types of safety equipment are items that protect the eyes, ears, mouth and overall body.
Eyes
If someone is working with chemicals, it is required that goggles, not just glasses, are worn. This helps keep out any vapors or splashes. If someone is working in an area with or near radiation, there are a few different options that can be used:
- Special-purpose safety glasses
- Goggles
- Face shields
- Specially designed helmets
|
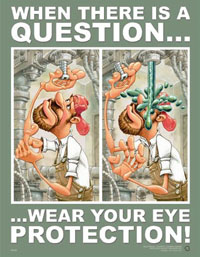 |
Protecting your eyes is more than just putting on an ordinary pair of glasses. Thorough research is necessary to make sure that the protective eye wear you choose will properly protect the eyes from any potential hazard. Make sure there are eye washing stations in every hazardous area in case there is an accident.
Ears There are many instances in which ear plugs or over-the-ear earmuffs may need to be worn in the workplace. Some of the jobs that would require wearing ear protection are:
- Factory worker
- Airport ground staff
- Construction worker
- Landscaping
- Event staff (such as concerts)
- Shooting range
Each one of these professions might have different requirements for the level of hearing protection needed. OSHA recommends that no one spend more than eight hours at 90 decibels or higher. Once the decibels reach 115, an employee should spend less than 20 minutes in that environment to avoid hearing loss. With proper ear protection, employees can work in these environments for longer periods of time. For low decibel jobs ear plugs will work just fine, but for higher decibel jobs you will need to invest in higher noise-cancelling earmuffs. For example, working with airplanes is one of the loudest jobs; an airline jet engine produces 140 decibels. These jobs require the strongest type of earmuff protection. There are earmuffs available that can be connected directly onto hard hats in the event that an employee would need multiple types of protection for their job.
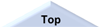
Breathing When it comes to working in potentially hazardous environments, it is very important to protect your lungs from any harmful debris or toxins. For example, concrete and masonry products contain silica. Silica is a hard, unreactive, Here and colorless compound that is a principal constituent of sandstone and other rocks. Since these products are one of the primary materials for construction, construction workers can be easily exposed to and inhale crystalline silica during activities such as the following:
- Chipping, hammering, and drilling rock
- Loading, hauling, and dumping of rock
- Abrasive blasting of concrete (regardless of abrasive used)
- Sawing, hammering, drilling, grinding, and chipping of concrete or masonry
- Demolition of concrete and masonry structures
- Dry sweeping or pressurized air blowing of concrete, rock, or sand dust
|
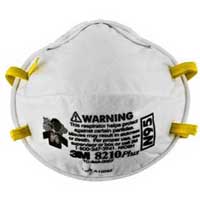 |
Even materials containing the smallest amounts of crystalline silica can be hazardous if they are used in ways that produce high dust concentrations
Body
We all know that construction workers are exposed to many hazardous materials on a daily basis, so it should come as no surprise to anyone that wearing protective clothing and equipment is a must. Protective clothing is an important means to prevent injury. Ideally, the best approach to avoiding injury is by having all hazardous materials safely removed by a professional team, however, working with hazardous materials for some people is just part of their job. As a result, it is of utmost importance to ensure that the equipment provided to your workers is not only reliable and effective but also properly used and maintained. Here are a few examples of protective clothing that a professional should consider from the Occupational Safety & Health Council: |
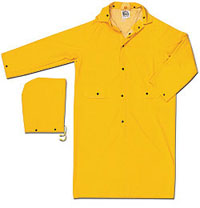 |
- Heat-resistant work clothing/aprons: Used in welding to prevent burns from the sparks of fragments and flying molten metals
- Anti-electrostatic work clothing: Suitable for workplaces where flammable materials are handled or where static charges might affect the quality of electronic products
- Life jackets: Used in workplaces near large bodies of water to reduce the risk of drowning if an employee should fall into the water
- Reflective clothing: Used for working in busy traffic; This clothing is brightly-colored and reflective in order to increase the visibility of the person wearing it and therefore, reduce the chance of being struck by vehicles or machinery
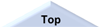
Permission and Supervision for Non-Professionals Hazardous areas should only be accessed by professionals that have been trained to safely maneuver around in and work in these areas. It is very possible for there to be many hazardous and dangerous materials within the area that may cause serious harm to you. There are times even when an area can be potentially hazardous for professionals, so if you are not professional, it is imperative that you seek permission from someone who is in charge to be there. When asking for permission, the person in charge will be able to determine if the area is safe enough for you access. Once the trained professional has deemed the area safe, he or she will then be able to escort you through the area. This is a common occurrence when dealing with home construction or renovation. Frequently, people will want to visit the construction site of their home. While most professional construction workers have no problem with clients visiting the site, it is imperative that you only access the construction site with a member of the construction team.
Never Appropriate for Children Although it seems obvious, it's important to note that it is never appropriate for children to be in or around hazardous sites. If for some reason you must bring a child or children to a construction site, it is recommended that children be left within a safe distance with a supervisor.
- Don't climb fences around or near construction sites.
- Don't play around loud construction sites.
- Don't play around construction sites with considerable air debris.
- Don't play around construction sites where demolition is involved.
- Don't fly kites around construction sites.
- Don't play in water near construction sites.
- Don't play near construction site refuse.
- If you see construction materials, like boards, nails, etc. let an adult know immediately.
- If you see a child breaking any of these rules, let an adult know immediately.
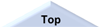
Conclusion Workplace accidents can happen in the blink of an eye and when you least expect it. Some can be easily identified and avoided, while others can potentially create dangerous situations for everyone. It is very important for employers to provide their employees with the appropriate training, knowledge, and protective gear. When you have worker's lives in your hands, you can never take too many precautions. There are many resources online to help educate you further in this. Please take the necessary steps in assuring that everyone is safe.
When someone is working around chemicals in an area that has flying particles, objects or dust, it is vital that they wear safety goggles. The type of work and the type of potential hazard dictates what type of goggles should be worn. Some types of jobs that would require safety goggles would be:
- Mining
- Electrical work
- Plumbing
- Welding
- Auto Repair
- Carpentry
- Manufacturing
- Construction
|
Texas America Safety Company |
4400 Danhil Drive |
Brownwood, TX 76801 |
|
Toll Free 1-800-646-5346 |
Outside US 1-325-646-5346 |
Local 325-646-5346 |
Fax 1-325-646-3790 |
sales@tasco-safety.com |
|